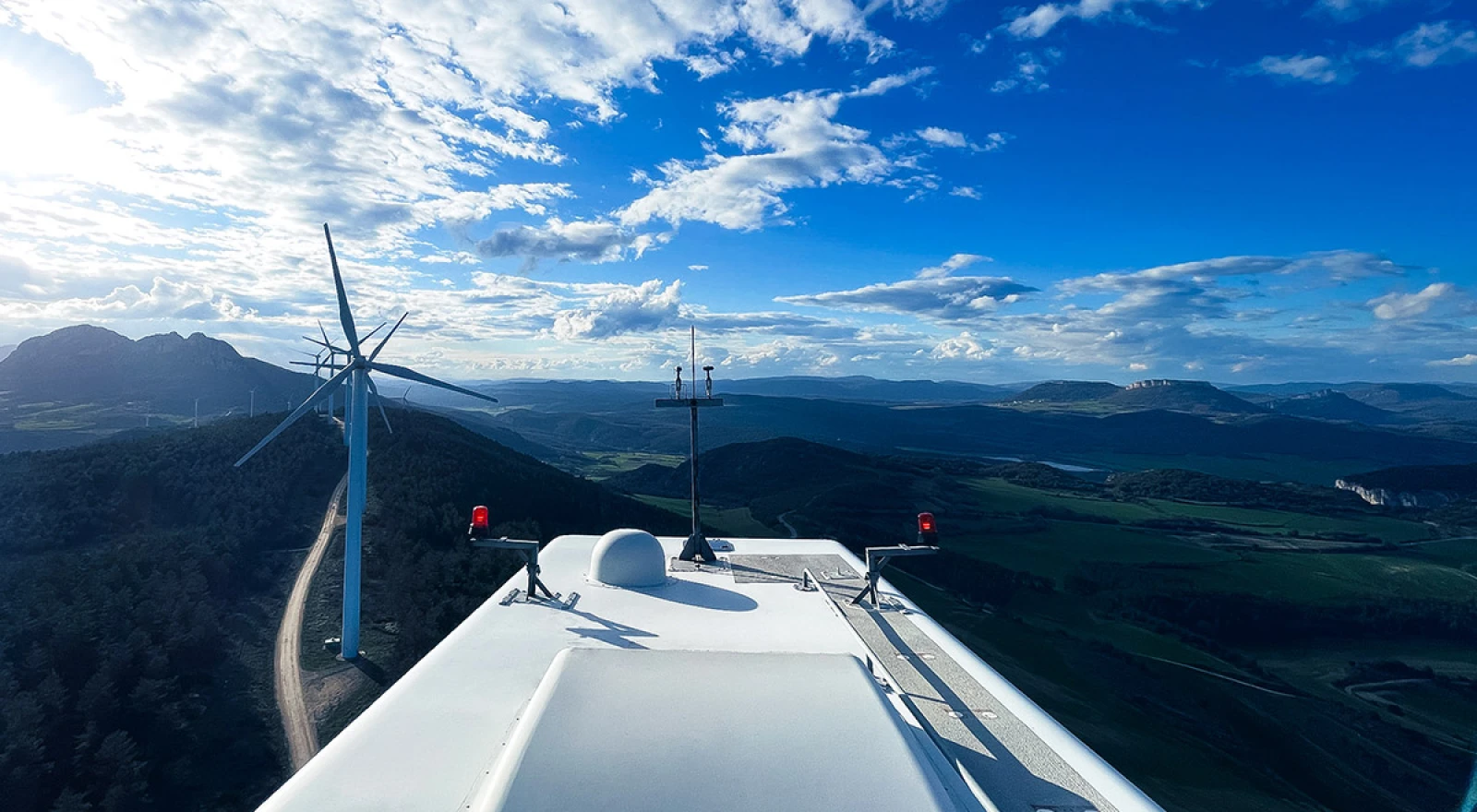
Perhaps you have asked yourself before a new, idle wind turbine, why it has been idle for weeks, despite the wind, shortly after completion and commissioning.
One of the main reasons is the so-called tonality, the oscillation of plant segments in a specific frequency that can be perceived very well by the ear, which is why plants cannot obtain an operating permit according to the IEC 61400 standard. The subsequent cause control of a decommissioned plant is always associated with very cost-intensive immediate measures. The EU-funded research project Eureka-Alarm by turbine manufacturer Senvion, Novicos and other partners is now intended to effectively prevent such tonalities already during turbine development.
When the plant that has just been put into operation comes to a standstill due to tonality problems, the operator and developer must immediately solve the following questions: "Which subsystem of the plant is causing the tonality and what are the costs and time involved in eliminating it?"
The sound emission of wind turbines is characterized by different physical processes, such as sound excitation, sound transmission, sound radiation and sound decoupling. These processes still take place on different levels of concretization, which is a real challenge for the acquisition and analysis of the system properties by means of existing measurement methods.
In the age of Industry 4.0, there was thus a desire to exploit the possibilities of the "digital twin" to reduce costs by eliminating these tonal effects. Figure 1 shows typical sound transmission paths.
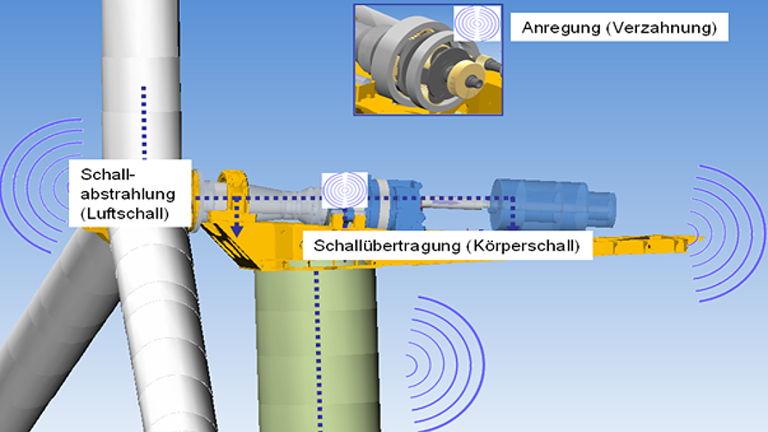
The digital twin as a solution
The digital twin is a virtual computer image of the real wind turbine that is identical down to the last design feature. Exactly this clone of a turbine and the reproduction of the real behavior, mainly with regard to the vibration behavior and the acoustic radiation, was the project objective in order to derive remedial measures.
In order to breathe life into a system, even if it is a digital one, a description is needed of what "the life" of a system actually is. "It is like a computer game in which each person is assigned a character trait and then interacts with others according to that trait's criteria. The more descriptions and variance the people in the game have, the more realistic their movements are in the game, the more exciting and successful the game will be on the market," explains Dr.-Ing. Olgierd Zaleski, CEO of Novicos.
It is no different for engineers who develop such simulations. The only difference is that instead of character descriptions of people, they have at their disposal data material from various measurements, some of them newly developed, and material characteristics of the system components. For this purpose, on the data basis of a design in the computer (CAD data) for each important design detail whose behavior is in interaction with other mechanical system components is described.
In simulation language, this process is called modeling. The interaction, i.e. the exchange of forces as excitation between mechanical systems, is determined in so-called multi-body simulations. It was suspected before the start of the project that existing modeling techniques could numerically predict sound propagation in complex systems and thus support the development process in early phases by providing important sound emission data. Unfortunately, however, neither a sufficient database nor a suitable elaborated overall model existed for wind turbines at that time. However, it is precisely the consideration of the overall acoustic model behavior that is one of the most important statements of the twin.
From a business perspective, timely results of design variants are the gain of the digital twin.
Calculation results that take months to produce are therefore only accepted in exceptional cases in today's world of ever shorter development cycles. With the currently available algorithms and typical hardware and software tools, simulation computing times of several weeks would probably have been required. It was therefore intended in the research project to develop subsystem models and improved computational algorithms to greatly accelerate the calculations. In order to achieve the core characteristic of the twin with fast deliveries of results, so-called transfer functions of intercoupled main components of the system, as shown in Fig. 2 and Fig. 3, were used.
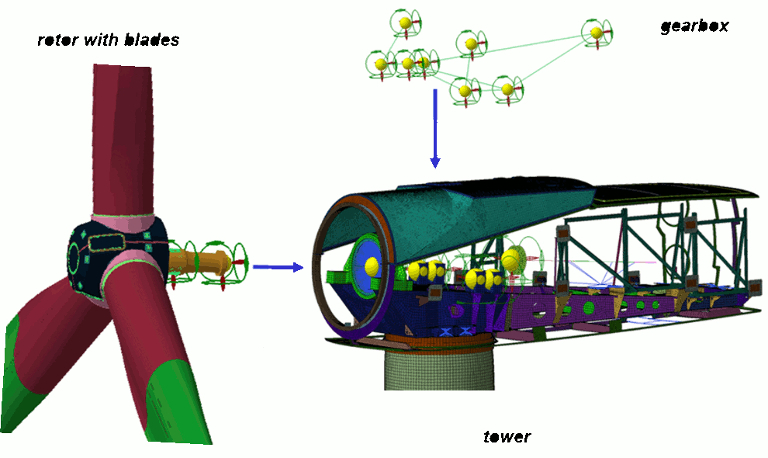
These were validated with measurements of transfer functions on a real system. In simplified terms, transfer functions describe how the vibrations generated by a system, for example the gearbox in the tower, are transmitted. With these transfer functions and the clustering, the division of the plant into different components, the simulation could already be accelerated considerably. What was still missing was a fast method of calculating how the plant as a whole radiated acoustically from the components. To simulate the sound radiation of a wind turbine, Novicos developed an acoustic model. The boundary element method was used. The entire surface mesh of the rotor, nacelle and tower has approximately 4 million elements. A section of the BEM meshing is shown in Figure 4. The very fine meshing shown results from the frequency range targeted in the project.
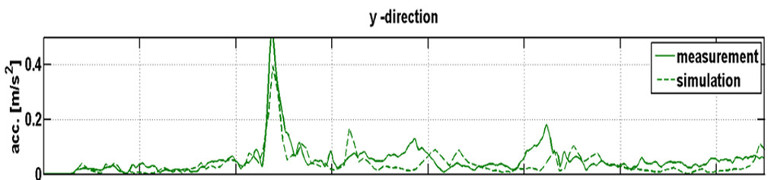
Only with the new calculation methods developed by Novicos in this project can models the size of a WKA currently be calculated with sufficient physical accuracy.
Dr.-Ing. Marian Markiewicz,Managing Director Novicos: "Within the framework of the project, stable block approximation algorithms for hierarchical H-matrices were developed and implemented so that system matrices to arbitrary networks can be generated with a stable approximation error. From the user's point of view, this means, in simple terms, that computational memory and computational time could be minimized by a factor of 1000 using these new mathematical descriptions."
Also effects of the ground regarding the sound radiation of the plant could be considered by so-called "impedance boundary conditions". This led to a further reduction of the computational effort and the modeling processes.
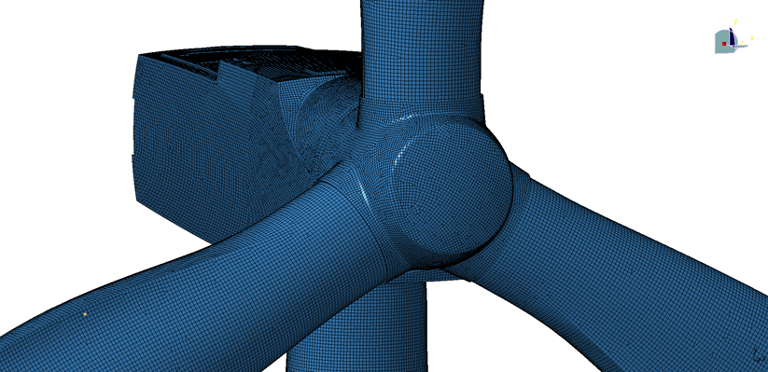
The result and further prospects
With such a simulation method in the digital twin, which has been validated by practice, plant manufacturers now have a way to determine the sound radiation of plant components at an early stage and to determine the effects of the individual components on the overall sound radiation. In the project, for example, the non-linear vibration behavior of elastomeric bearings in a specific frequency range was determined. With this knowledge, it was possible to introduce concrete measures to counteract tonality. Requirements for suppliers and vendor parts can thus be validated at an early stage. With cost reduction in mind, optimization measures on the manufacturer and supplier side will thus become more efficient in their application in the future. The calculation results (exemplified in Fig. 5) within a period of a few days now allow this.
The consideration of quality influences on the vibration properties in the manufacturing process also allows such close dovetailing of development with the subsequent production process. It is another approach to saving costs at an early stage and investing in optimization measures in a more targeted manner.
The new simulation method for the radiation behavior of large structures developed in the project is now being used at Novicos for the development of other digital twins, such as ships. The methods are to be further developed in the near future so that moving sources, such as aircraft, can also be calculated with them.
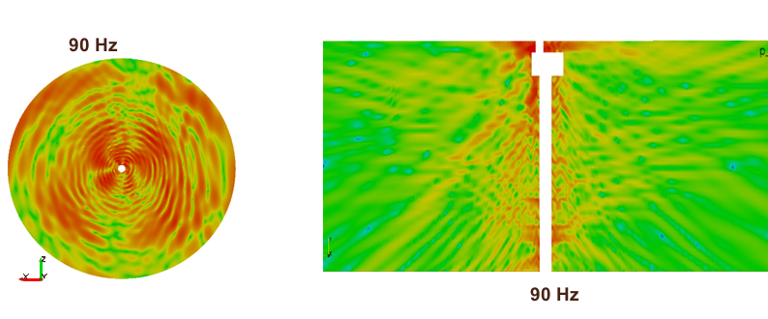
Do you have questions about this article?
I will gladly be there for you and answer your questions.
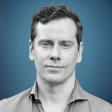